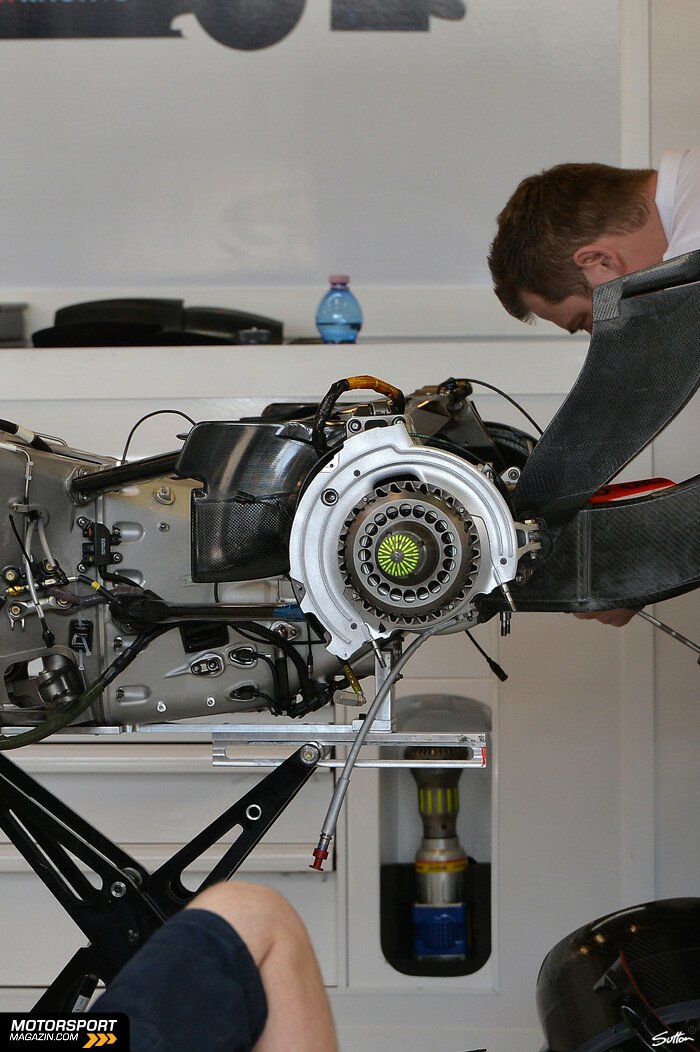
It saves time and resources when manufacturing parts, especially those likely to have high rates of development. You're allowed more flexibility if you don't have to fabricate an entire nose/wing assembly just to update a portion of the wing. The big change in regulations governing those components means specifications for both are likely to change frequently as the team hones the overall design of the car.Gridlock wrote:Another silly question; is it usual to have a detachable footplate like all those noses demonstrate? Not a familiar sight to me, noses with no FW attached - I assumed they were generally one piece, to reduce weight.
You'll notice the floor around the rear tyre is detachable too for the same reason.bhallg2k wrote:It saves time and resources when manufacturing parts, especially those likely to have high rates of development. You're allowed more flexibility if you don't have to fabricate an entire nose/wing assembly just to update a portion of the wing. The big change in regulations governing those components means specifications for both are likely to change frequently as the team hones the overall design of the car.Gridlock wrote:Another silly question; is it usual to have a detachable footplate like all those noses demonstrate? Not a familiar sight to me, noses with no FW attached - I assumed they were generally one piece, to reduce weight.
Looks like a continuation of a theme seen on last year's FW35 and others.humble sabot wrote:I was hoping it would be lighter than the dark blue in testing, hopefully it would reveal something. And reveal it has.![]()
I was sure there was a little more going on at the nose than we could see in the dark paint.
Be careful how you word it, there are many variations of leading edge devices. For this please use leading edge slot because that is what it is.marcush. wrote:The Leading Edge flap with its Limited range of airspeeds wehre is would work is something worth developing methinks. My Impression is you want to be able to Feed the Maximum Air Maß at lower Speeds But be able to Redirect the Surplus not needed at full Speed making it do other work( Helbing Keep Flow attached on the sidepods?)
That is exactly what you need to avoid, remember if the airflow stalls flowing around the sidepods then the airflow instantly becomes turbulent. Wings and other downforce generating devices can do very little with turbulent air. Note that turbulent air is not necessarily the same thing as spinning vortex airflow. However usually after a vortex breaks down it leaves a large amount of turbulent air in its wake.rjsa wrote:It doesn't make sense pulling air out of the intake and directing it over the sidepod, oit's not like you need to avoid the sidepod to stall or anything like that.
I'd make a wild guess and say it's just a bunch of different intake cowlings, with different opening sizes, that do not fit that well to the sidepod but are intended on running tests on heat dissipation.
You mean air will be pushed through the slot, i.e. flow from inside the sidepod to outside the sidepod?trinidefender wrote:[...]
Unfortunately they don't work like that. Air will still be pulled through the slot as a result of lower pressure above the sidepods and higher pressure in the ram air sidepod intake. The only way, that I can see at least, for your idea of diverting more cooling air at low speeds then at higher speeds having more air going through the slot would be with mover able aero which is obviously banned.
[...]